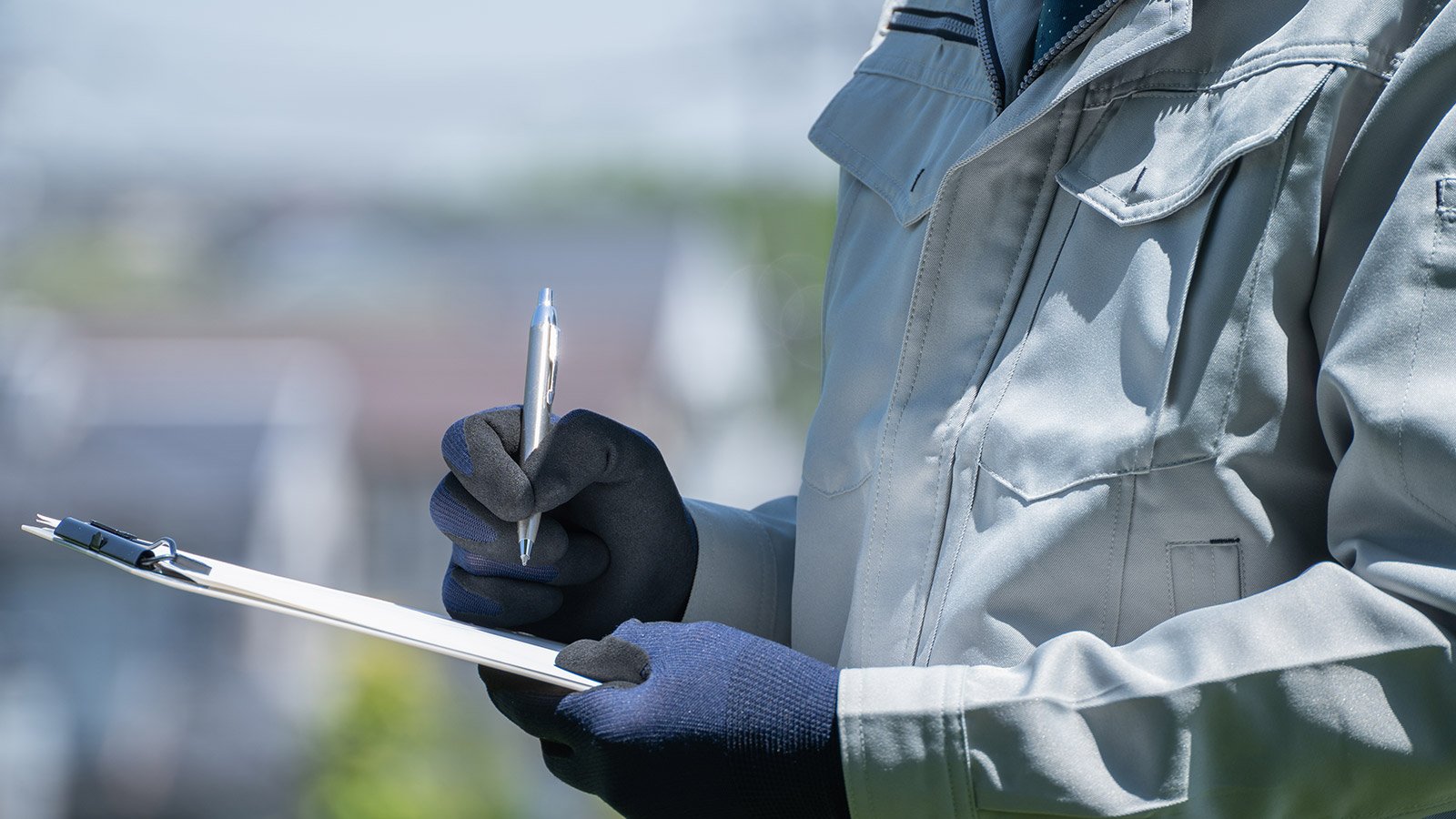
Published September 19, 2022 | 4 minute read
Published September 19, 2022 | 4 minute read
Mechanical seals are an essential component in virtually any industrial pump application, and properly inspecting them regularly will help keep your processes and critical equipment operating smoothly.
Sunair Co. supplies a range of top mechanical seals from the most dependable brands on the market, and our highly trained team of specialists is here to identify and remedy seal performance issues before they become problems. This helps ensure their integrity and optimal functionality.
Mechanical seals contain pressurized fluid or gas and prevent leaks and contamination to your process fluid. They primarily consist of a rotary seal face with a driving mechanism, stationary seal face, tension assembly, sealing gaskets, and O-rings or elastomeric bellows.
These seals are most commonly used in industrial applications for rotating equipment, like centrifugal pumps, compressors, mixers, steam turbines, and blowers.
When mechanical seals fail, malfunction, or are otherwise installed improperly, they can pose a significant risk to your team and facility’s safety, the effectiveness of your equipment, and overall performance of your operations.
Like all mechanical components, the chances of mechanical seal leakage and failure increase over time. Addressing the problems caused by mechanical seal failures—such as repairs or pump equipment replacement—can lead to costly operational downtime. Depending on the material handled, this can also pose safety risks for your end products and staff.
Regularly conducting mechanical seal inspections and monitoring differences in performance will help keep your seals and pumping operations working optimally for longer. Instituting scheduled or routine inspections can result in prolonged seal life, better performance, improved safety for your crew and facilities, and reduced pump maintenance costs.
You could perform basic monitoring with your in-house team, but if personnel are untrained or inexperienced in conducting a proper inspection, it could result in significant and expensive problems. If you need mechanical seal inspections, it’s best to enlist experienced and trained professionals such as Sunair’s team of experts.
We can assess your facility’s equipment and identify when your seals need repair or replacement. Our high-grade, factory-authorized repair and installation services will outfit your operations with the right mechanical seals for your needs or restore your existing seals for prolonged performance.
Some of the factors which could contribute to seal failure include operating a pump off its curve—which leads to high vibration—pipe strain, poorly designed or improperly grouted baseplates, cavitation, misalignment, dead-head, and dry-running. Various operating conditions can shorten seal life, as well, because the changing load on the shaft affects deflection, which can disturb the seal.
Be sure to familiarize yourself with all of the operational factors and conditions that could adversely affect your seal equipment. Here are several beneficial steps to conduct a basic mechanical seal inspection:
Mechanical seal inspections need to be conducted while the pump equipment is not in operation, so scheduling them during your regular pump maintenance can help you save on downtime.
Be sure to avoid dry-running your pumps as this can cause significant wear on your mechanical seals. Also–be aware of applications with insufficient vapor pressure margins, which can also cause dry-running at the seal faces.
Operations involving high vibrations can deteriorate and misalign your seal components, so reducing these and ensuring proper installation is paramount. In dual- and non-pressurized seals with barrier or buffer fluid, regularly inspect the fluid level to ensure long-lasting performance.
Sunair recommends Royal Purple barrier fluids, which are ultra-clean, FDA approved, and optimal for most mechanical seal applications.
Mechanical seals are an indispensable component of fluid handling and your choice in mechanical seal manufacturer could make a huge difference in your overall operational efficiency, as well as the safety and productivity of your facilities.
That’s why at Sunair Co., we pride ourselves on working with some of the highest-quality and most reliable manufacturers in the industry, including AESSEAL, one of the leading producers of mechanical seals and support systems in the world.
Our experienced team of specialists provide a range of repair and maintenance services for various pump equipment and components, including mechanical seal inspections and repairs.
No matter what your operations require, we can assist with performing pump and mechanical seal audits and energy assessments to help you identify opportunities to extend operating life and reduce total cost of ownership.
Receive the latest industry news, once a month. Unsubscribe anytime.
To determine the size of a component mechanical seal, measure the inside diameter of the seal face, the length of the spring, and diameter and thickness of the stationary seat.
Read NowDesigned to handle various hydrocarbons in accordance with the high standards of the American Petroleum Institute, API pumps ranging from end suction to vertical turbine models are commonly used in the petroleum, petrochemical, and natural gas industries.
Read NowSunair Co. carries high-quality propane pumps and compressors from leading manufacturers such as Sundyne, Blackmer, and National Pump to ensure your operations perform safely and effectively.
Read NowAir-operated double-diaphragm (AODD) pumps utilize compressed air and dual chambers to transport fluids safely and efficiently in support of a wide range of industrial applications.
Read Now2475 Wyandotte Road
Willow Grove, PA 19090
Phone: (215) 657-9800
Fax: (215) 657-9881
Email: sunairco@sunair.com
© Copyright 2025 Sunair Co.
Logos on this page are copyrights of their respective companies. The Sunair logo is a registered trademark of Sunair Co.
Leave a comment