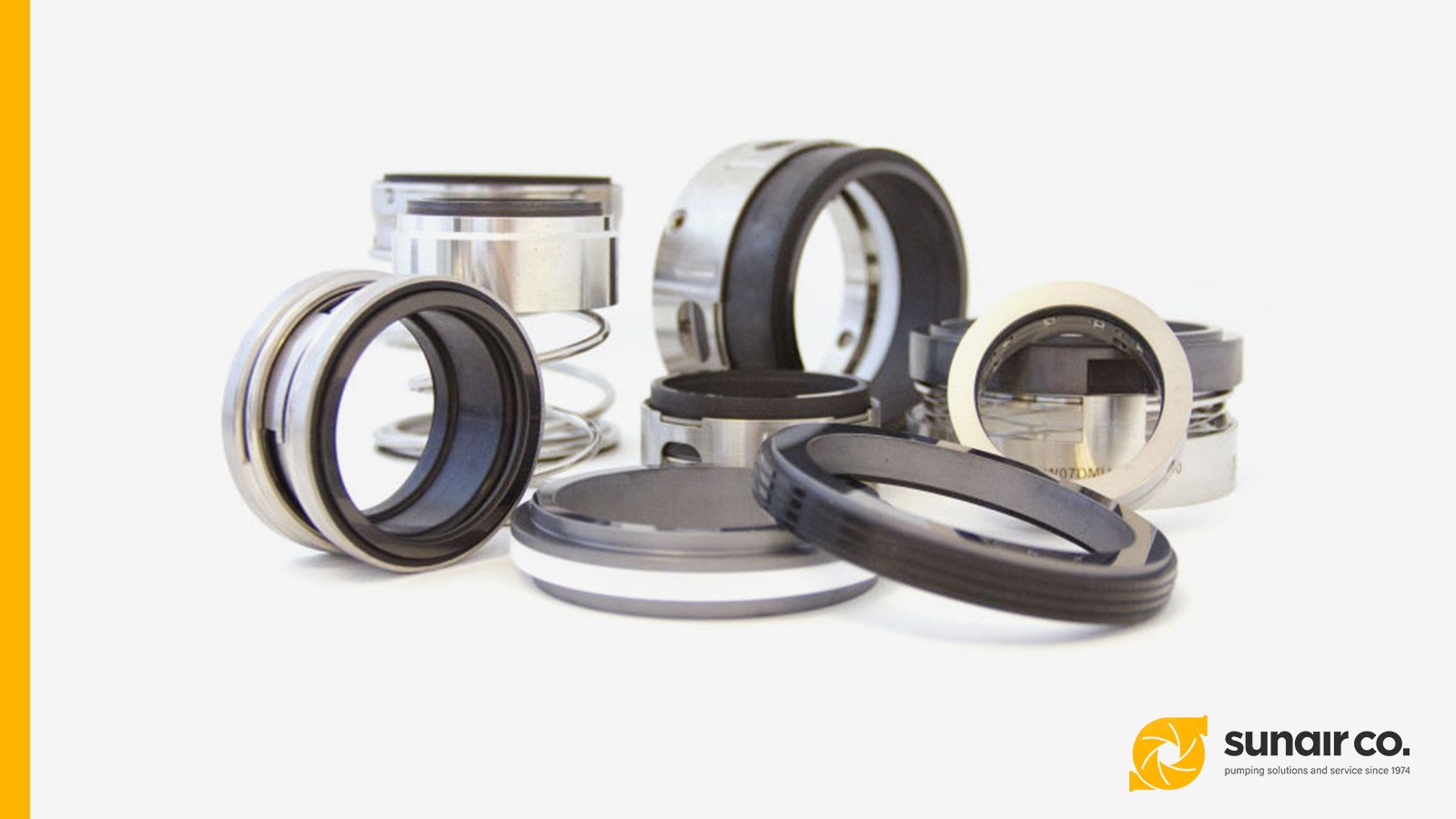
Published September 09, 2021 | 3 minute read
Published September 09, 2021 | 3 minute read
Now that you have the right pump for your application, you need a mechanical seal to guarantee your processes run without a hitch. Seals are a critical component for a vast array of industrial and commercial applications, preventing both leakage and harmful emissions.
So – how do you ensure that you have the right seal for your pump?
Here’s what you need to know about measuring your mechanical seal…
Mechanical seals are devices designed to prevent the leakage of fluids and gases during transport through rotating equipment, such as pumps and mixers. They are typically comprised of both stationary and rotary components, which together establish a secure seal.
There are many types of mechanical seals, with various designs, arrangements, and materials to handle liquids and gases at a variety of pressures, temperatures, and speeds.
Mechanical seals are essential parts of industrial pumping processes. To maintain a controlled flow of liquid, prevent leaks and cross-contamination, and sustain a high level of cleanliness, using the right seal is a must.
The seal face is affixed to and rotates with the shaft to seal against the stationary element.
The secondary seals provide sealing around the mating ring, gland, and in the housing.
Stationary seats are mounted in the housing and do not rotate with the shaft.
Springs or other mechanical loading devices are incorporated to exert axial force, maintaining a static seal when the pump is not running.
To accurately measure your mechanical seal, you must separate each component and calculate its dimensions individually:
Once you have your measurements, identify and cross-reference the appropriate seal for your application.
Now that you know how to measure your mechanical seals, the next step toward determining what mechanical seal you need is to verify it meets the correct design and material requirements for your processes.
A cartridge seal is a self-contained unit housing the sealing components, pre-assembled and preset by the manufacturer. These can be equipped with one or two seals, depending on the usage.
A component seal consists of a separate rotating unit and stationary seat mounted in a housing.
A gas seal does not use a wetted barrier fluid, so the seal faces operate only on a thin film of air or nitrogen. These are primarily installed in applications where maximum protection against leaking or contamination is required.
Mechanical seal materials can determine whether it functions properly and how long it will last before requiring maintenance. The primary sealing surfaces are typically made from hard material, such as silicon carbide, ceramic, or tungsten carbide, in conjunction with a softer material, such as carbon. Many others can be used, depending on pressure, temperature, and chemical properties of the liquid inside.
Whether you’re selecting from a line of standard cartridge seals, or seeking something a bit more specialized, Sunair Co. can equip you with exactly the seal you need.
Supplying everything from non-chemical external seals to cartridge-mounted double seals, and providing a full range of support systems, including fluid distribution units, easy-clean systems, and myriad other configurations, you can trust Sunair Co. to keep your processes running smoothly.
Sunair Co. is the industry-leading expert on mechanical seals, pumps, compressors, and more. Our team has been developing custom systems and advising clients on which mechanical seals they need for their systems, across dozens of industries and hundreds of applications, for nearly 50 years.
Receive the latest industry news, once a month. Unsubscribe anytime.
Designed to handle various hydrocarbons in accordance with the high standards of the American Petroleum Institute, API pumps ranging from end suction to vertical turbine models are commonly used in the petroleum, petrochemical, and natural gas industries.
Read NowRegularly inspecting your mechanical seals and monitoring various factors that could contribute to failure or leakage will help extend their lifespan, while ensuring operational efficiency and safety.
Read NowSunair Co. carries high-quality propane pumps and compressors from leading manufacturers such as Sundyne, Blackmer, and National Pump to ensure your operations perform safely and effectively.
Read NowAir-operated double-diaphragm (AODD) pumps utilize compressed air and dual chambers to transport fluids safely and efficiently in support of a wide range of industrial applications.
Read Now2475 Wyandotte Road
Willow Grove, PA 19090
Phone: (215) 657-9800
Fax: (215) 657-9881
Email: sunairco@sunair.com
© Copyright 2025 Sunair Co.
Logos on this page are copyrights of their respective companies. The Sunair logo is a registered trademark of Sunair Co.
Leave a comment