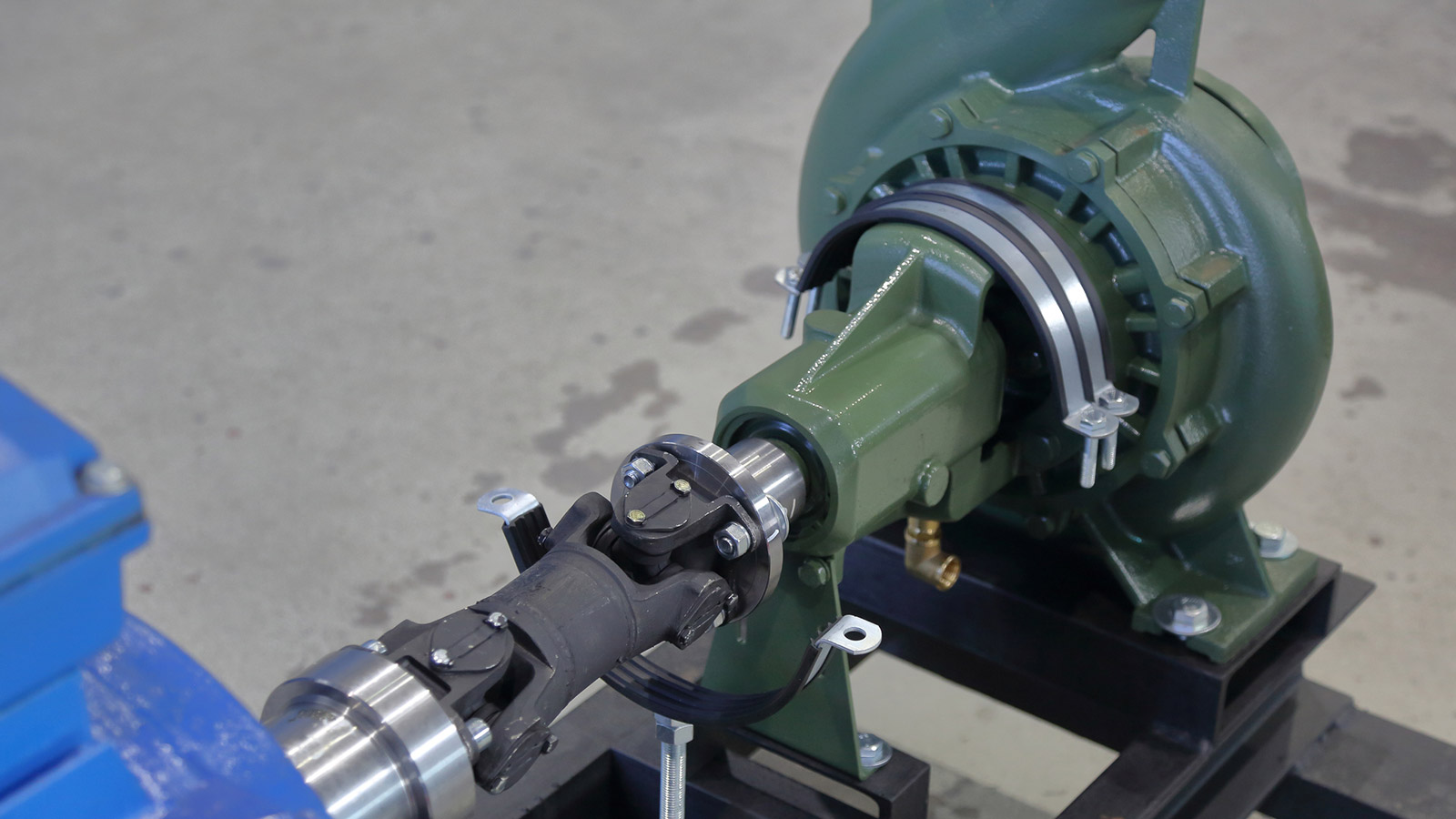
Published July 08, 2025 | 7 minute read
Published July 08, 2025 | 7 minute read
Your ANSI pump is the workhorse of your industrial process, silently moving fluids day after day—until something goes wrong. How do you know when that trusty pump has reached the end of its serviceable life? At what point do continued repairs become more costly than replacement?
The repair-versus-replace decision directly impacts your operational reliability, safety, and bottom line.
While repairing may seem more economical in the short term, there comes a point when replacement makes better business sense. For instance, the initial price of your industrial pump is only 10% of its total cost when employed at your plant for the 15 to 20 years it typically lasts, with the rest of its cost coming in the form of installation, energy, downtime, and maintenance, according to the nonprofit Hydraulic Institute.
The following critical indicators will suggest when it's time for retirement rather than rehabilitation.
Mechanical seals represent the most vulnerable component in your ANSI pump, accounting for upward of half of all pump failures. While occasional seal replacement is normal maintenance, frequent failures indicate underlying issues that repairs alone won't fix.
Keep in mind: All pump seals leak as a way to maintain a reliable film closure, but excessive amounts signal that it’s time for replacement.
Mechanical seals must maintain precise face contact with minimal deflection to prevent problematic leakage. The ANSI/ASME B73.1 standard specifies a maximum allowable shaft deflection of 0.002 inches at the seal face to ensure proper seal performance. In aging pumps, cumulative wear to bearings, shafts, and seal chambers often creates conditions exceeding this threshold.
Acceptable leakage rates for mechanical seals are typically established:
An experienced industrial pump and mechanical seals provider can help you pin down whether your ANSI pump is exceeding the reasonable leakage rate. You always have to keep in mind downtime costs. How much risk are you willing to shoulder by holding off the replacement of a compromised mechanical seal or ANSI pump?
Plus, the longer you wait, the more time you give for potential safety hazards with hazardous or flammable liquids to develop.
While less visible than catastrophic failures, efficiency degradation silently drains your profitability with every operating hour. A pump’s efficiency can degrade as much as 10% to 25% before replacement, according to a study of industrial facilities commissioned by the U.S. Department of Energy (DOE). Efficiencies of 50% to 60% or lower are not uncommon, either.
ANSI pump efficiency declines progressively due to several factors:
Every increase in surface roughness reduces your hydraulic efficiency. When internal clearances double (a common wear condition), efficiency also drops below the original manufacturing specifications, funneling more from your profits at the end of the day.
Excessive vibration that persists despite repair attempts signals fundamental issues with your pump that typically cannot be economically resolved through continued maintenance. ANSI/HI 9.6.4 standard specifies maximum allowable vibration values based on your pump’s power rating. The standard also defines alert levels, alarm levels, and shutdown thresholds.
Vibration that exceeds these limits or continues increasing despite repairs typically indicates:
Excessive vibration dramatically accelerates component failure rates. Beyond component damage, vibration also creates fatigue stresses in piping systems, loosens connections (creating leak paths), and reduces seal life dramatically. Plus, it increases energy consumption and can damage adjacent equipment.
When several major components simultaneously exceed their wear limits, repair costs escalate dramatically, often exceeding the threshold—making replacement far more economical.
ANSI pumps contain several critical wear components, each with specific tolerance limits. A reliable industrial pump service provider can tell you whether your bearings, wear rings, impeller, shaft, or mechanical seal have become worn to the point of replacement.
Most manufacturers recommend the "50% Rule.” When repair costs exceed 50% of replacement costs, replacement becomes the economically preferred option. For ANSI pumps, specifically, this threshold may be even lower (40%) due to their standardized nature and competitive replacement market. Again, keep in mind: Slowed efficiency, potential downtime, and risk of damage to other components contribute to cost analysis when pushing your ANSI pump beyond when it should be replaced.
Multiple failing components create compounding problems:
The pump casing represents the most expensive single component and is often the limiting factor in ANSI pump lifespan. Over time, the pump casing weakens, due to cracks or erosion, which means it will no longer be able to withstand your system’s intense internal pressure. As a central component of your pump, its failure can have disastrous results.
So, when your casing develops significant damage, replacement typically becomes the only viable option.
ANSI B73.1 pump casings are designed with specific pressure containment requirements and typically include a corrosion/erosion allowance of approximately 1/8" (3.2mm). Once material loss exceeds this threshold, safety margins are compromised.
Critical casing issues include:
While each of these five signs individually suggests replacement may be warranted, their cumulative impact provides the clearest direction. When two or more of these indicators are present simultaneously, the replacement case becomes compelling from both economic and safety perspectives.
The most effective approach combines technical assessment with lifecycle cost analysis. Remember: Your purchase price typically represents only about 10% of total lifecycle costs, while energy, maintenance, and downtime account for nearly 70%.
By partnering with Sunair for your ANSI pump replacement, you can:
Sunair's structured evaluation program can help your maintenance team assess these five critical indicators across your pump inventory. Our factory-trained technicians specialize in ANSI pump diagnostics and can perform comprehensive assessments, including vibration analysis, efficiency testing, and mechanical inspections.
When replacement is the right choice, we carry an extensive inventory of ANSI pumps designed for chemical processing, petroleum refining, water treatment, and other demanding applications. Our installation teams ensure proper alignment, sealing, and system integration—ultimately improving your facility's bottom line and operational reliability.
Receive the latest industry news, once a month. Unsubscribe anytime.
To determine the size of a component mechanical seal, measure the inside diameter of the seal face, the length of the spring, and diameter and thickness of the stationary seat.
Read NowDesigned to handle various hydrocarbons in accordance with the high standards of the American Petroleum Institute, API pumps ranging from end suction to vertical turbine models are commonly used in the petroleum, petrochemical, and natural gas industries.
Read NowRegularly inspecting your mechanical seals and monitoring various factors that could contribute to failure or leakage will help extend their lifespan, while ensuring operational efficiency and safety.
Read NowSunair Co. carries high-quality propane pumps and compressors from leading manufacturers such as Sundyne, Blackmer, and National Pump to ensure your operations perform safely and effectively.
Read NowAir-operated double-diaphragm (AODD) pumps utilize compressed air and dual chambers to transport fluids safely and efficiently in support of a wide range of industrial applications.
Read Now2475 Wyandotte Road
Willow Grove, PA 19090
Phone: (215) 657-9800
Fax: (215) 657-9881
Email: sunairco@sunair.com
© Copyright 2025 Sunair Co.
Logos on this page are copyrights of their respective companies. The Sunair logo is a registered trademark of Sunair Co.
Leave a comment